Heute holte ich mir eine neue Tischbohrmaschine vom Zgonc. Ich habe lange überlegt und alle für und wider abgewogen und mich dann für dieses Gerät entschieden:
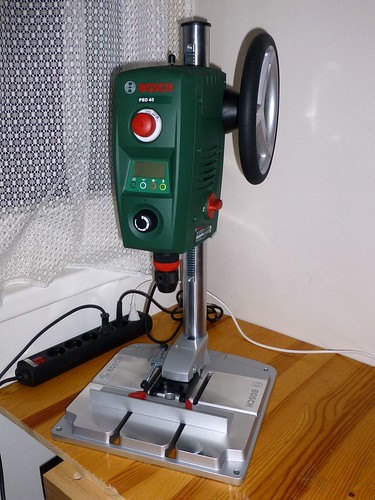
Für meine Verwendung schien dies das am besten passende Gerät. Da ich so gut wie nie Metall bohre stört auch die elektronische Regelung nicht (für solche Fälle habe ich ja noch mein altes, ratterndes und riemengetriebenes Standbohrgerät).
Besonders gefallen mir:
- Beleuchtung
- Werkstückhalter
- Laser (gerade nach drei Augenoperationen tu ich mir mit dem räumlichen Sehen noch sehr schwer und da erleichtert der Laser das richtige Ansetzen enorm)
- Tiefenanzeige
- Werkzeugloser Bohrerwechsel
- der leise Lauf
Minuspunkte:
- noch keine gefunden
Auf eine alte Platte (im Keller beim Sperrmüll gefunden) befestigte ich eine Leiste. Mit dieser wurde die Platte an der Werkbank festgeklemmt. Bei Gelegenheit schraube ich die Bohrmaschine noch an der Platte fest. Da ich platzmäßig sehr beschränkt bin kann ich so im Bedarfsfall schnell mal Platz schaffen und die Maschine auf die Seite räumen.
Ich hoffe, ich komme demnächst dazu die Maschine zu testen. Mal sehen, ob ich dann den einen oder anderen Kritikpunkt finden werde. Wie auch immer, ich werde berichten.